With the expansion of cities, it is necessary to install sewerage systems to prevent waterborne diseases. By 2016, about 680 million people were served by the sewerage system. Depending on the geographical environment of the area, the collection system uses gravity to move wastewater down the drain or uses a pump station to force the transfer of wastewater to a centralized treatment plant at a high altitude and a certain distance.
The valves in the pump station are located in the sump, dry or separate valve wells. Three types of valves commonly found in pump stations include check valves, globe valves, and exhaust valves. The purpose of the sanitary check valve is to prevent reverse flow when the sanitary pump is closed; the sanitary shut off valve is used for isolation when maintenance or repair is required; the exhaust valve mainly provides flow efficiency and minimizes surge. The selection of valve applied to wastewater is similar to the selection of the pump, and the solid content of the flow medium must be considered.
When the pump is not running, the check valve is essential in the pump station to prevent backflow. There are many types of check valves that are essential to the effectiveness of wastewater treatment services.
Swing check valve
Swing check valves are the traditional choice and are made of cast iron with a corrosion-resistant interior. When swinging the check valve seat to a 90-degree seat, there is usually a lever and weight to assist in closing and provide position indication. The valve can also be equipped with a spring, air cushion, or oil damper arrangement to reduce valve opening and closing effects. Traditional swing check valves are spring hinge designs that greatly reduce pop problems, especially in high lift applications. The additional benefits of flexible hinge design include a corrosion-resistant disc, an encapsulated hinge pin, position-indicating options, and a top mount for easy maintenance.
Ball check valve
Ball check valves are typically used for smaller systems at a lower cost. The valve USES a ball (as opposed to a disc) as its closing part, which is raised and closed through flow during system operation. When the pump is closed, the ball falls back into the closed position. Ball check valves can be installed in both horizontal and vertical lines.
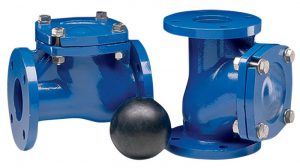
Pump control check valve
Pump control check valves and special surge equipment may be required when the main pump is at a high head or pump fluid through a long delivery distance, rather than traditional check valves. The pump control check valve is provided with an electric, pneumatic, or hydraulic actuator and electrically connected to the pump loop. Pump control valves open and close for a few minutes, slowly changing the speed of the fluid to prevent surges in long power supplies. In addition, pump control check valves can be used to significantly save power consumption due to their low head loss.
Automatic exhaust valve
The automatic exhaust valve is often installed in the pump discharge. These valves are automatic and open to discharge air when the air is gathered in the body. When wastewater enters, float and close the disc to close the orifice so that the fluid is not expelled. The waste air valve is often characterized by a slender cone to prevent clogging and a sloping bottom to facilitate drainage, and the type 316 stainless steel internal components to withstand corrosive wastewater and sewage gases. The importance of the exhaust valve cannot be ignored. Not only do they maintain the flow efficiency of the pipe and accumulate air through the exhaust, but they also perform many other functions, including the rapid recognition of air after a pump power failure to prevent the surge control of the vacuum bag formed during the column separation process.
Please visit http://www.adamantvalves.com/ for more information.